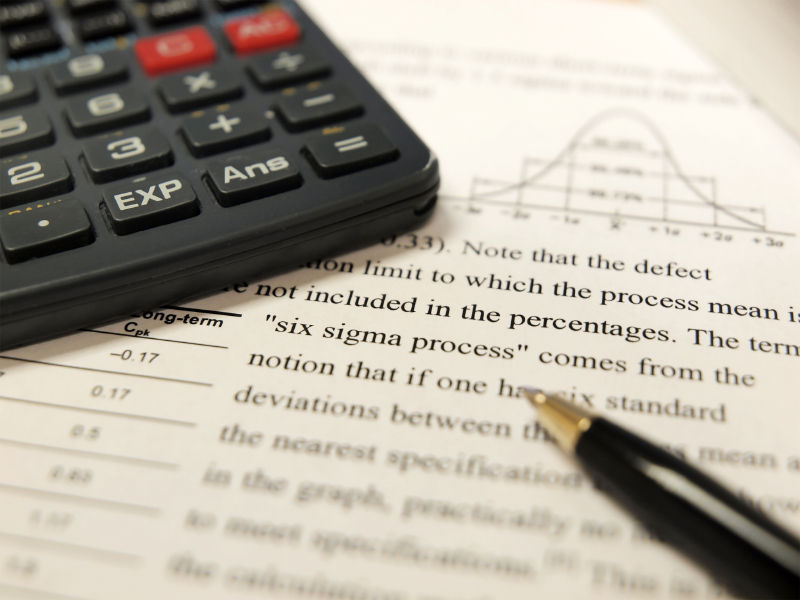
In manufacturing, most companies have to deal with costly quality problems eating up too much of their profit. Many of these problems persist for far too long because problem solving can be difficult. When the issue is solved, it always seems easy with hindsight. But until it is solved, there are a lot of potential root causes. All of the candidates for root cause seem reasonable during the brainstorming stage and with many of them, it can seem overwhelming. Each candidate root cause needs to be investigated. Your approach will rank them in order of likelihood or group them so that a single test can keep or rule out more than one of them. Either way, it's a lot of work.
The randomness of Quality problems is another reason why they are often abandoned. When something happens at random, it's tough to know why. Sometimes, randomness isn't a feature of the process, it's a feature of our detection. Consider the following examples;
Company A experienced underweight problems with a food product.
Company B experienced overweight problems with a continuous manufacturing process.
Company C experienced failed test results with a chemical product.
All observed these results randomly and so the problem was thought to be random.
Company A - underweights showed up at final packaging. Each item is weighed before inserting into a box and many were rejected. Some days there were plenty, other days few, but never zero and never in any sort of cluster that might provide a clue. With this Six Sigma project, we needed to identify where each product came from upstream. There were several workstations on two assembly lines. Our approach used some small coloured papers that we could attach to the products and remove later, so as not to affect the process or product.
One of the workstations was a cutting station that cut large items into several smaller ones. Each cut item was given a different coloured paper. At weighing, several stations downstream, we learned that all of the defects were either the first cut or the last cut. Never any of the middle cuts. Now, it is no longer a random defect. It has a pattern. The Black Belt on this project was able to explore more precisely with this clue and solved the problem in a short time.
Company B - a continuous process yielded thousands of items every day and at a later stage of manufacture, many of these items were found to weigh too much and had to be scrapped. About 11% of them! Root cause was elusive because.....it was a random event. Well, not so fast. The detection of them was random but not necessarily the manufacture of them. We moved upstream and monitored the process where the raw materials came together and took a large number of these items and weighed them in the order that they were produced. We observed a pattern. A lag 3 serial plot showed a distinct correlation. This means that if a unit was high in weight, then the unit three items later would also be high in weight. And likewise, low weight followed low weight. Not every time but many times. It was structure and not random and provided a valuable clue. This clue was not on the list generated in brainstorming.
Company C was dealing with a chemical product that, after 100% inspection, resulted in 3% failures. These failures appeared randomly but they weren't generated randomly. As we moved upstream in the manufacturing process we started labelling items with small cards that contained information such as which workstation, which operator, 1st-2nd-3rd in line etc. The cards were filled out for a full shift and when we were collecting them at the final test station we discovered a vital clue. One process step was heat soaking in a large oven. The oven had 12 shelves but every failed item came from the bottom three shelves. No longer random. That clue lead to additional testing that showed the oven to be several degrees cooler at the bottom and so products were not being processed correctly.
Randomness in detecting Quality problems can be frustrating but treat these root cause investigations in the same manner that a detective would try to solve a crime. Go to the scene of the crime and search for clues.
Comments